In the fast-paced world of packaging, stick packing machines play a crucial role in ensuring products are efficiently packaged for distribution. These machines are designed to handle a variety of products, from powders to liquids, and are essential in industries such as food, pharmaceuticals, and cosmetics. However, like any machinery, they can encounter problems during operation. Understanding these common issues and their solutions can help maintain productivity and reduce downtime.
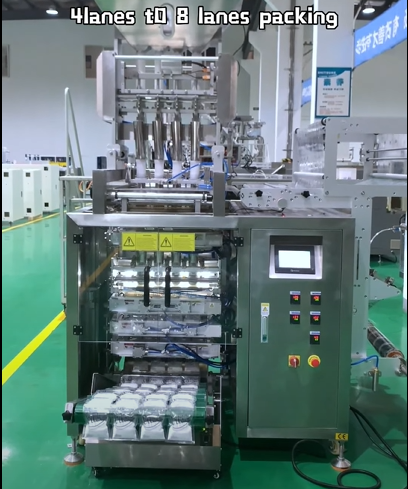
1. Inconsistent Sealing
Problem: One of the most common issues faced by operators of stick packing machines is inconsistent sealing. This can lead to product leakage, spoilage, and customer dissatisfaction.
Solution: To address this issue, operators should regularly check the sealing temperature and pressure settings. Each product may require different sealing parameters, so it’s essential to refer to the manufacturer’s guidelines. Additionally, ensuring that the sealing surfaces are clean and free from debris can significantly improve seal integrity. Regular maintenance and calibration of the machine can also prevent this problem.
2. Product Jamming
Problem: Product jamming can occur in multi-lane sachet packaging machines when the product does not flow smoothly through the machine. This can halt production and lead to wasted materials.
Solution: To minimize the risk of jamming, operators should ensure that the product is suitable for the machine’s specifications. Adjusting the feed rate and ensuring that the product is not too moist or too dry can help maintain a smooth flow. Regularly inspecting and cleaning the feeding mechanisms can also prevent blockages. If jamming persists, it may be necessary to consult the machine’s manual for troubleshooting specific to the model.
3. Incorrect Fill Volume
Problem: Achieving the correct fill volume is critical in stick sachet packaging machines. Incorrect fill volumes can lead to product waste and regulatory issues, especially in the food and pharmaceutical industries.
Solution: To ensure accurate fill volumes, operators should regularly calibrate the filling system. This involves checking the volume dispensed against a standard measurement. If discrepancies are found, adjustments to the filling mechanism may be necessary. Additionally, using high-quality, consistent raw materials can help maintain uniformity in fill volumes.
4. Machine Overheating
Problem: Overheating can occur in stick packing machines, particularly during prolonged use. This can lead to machine failure and costly repairs.
Solution: To prevent overheating, operators should monitor the machine’s temperature during operation. Implementing regular breaks can help cool down the machine. Additionally, ensuring that the machine is well-ventilated and that cooling systems are functioning properly can mitigate this issue. Regular maintenance checks can also identify potential overheating problems before they escalate.
5. Misalignment of Packaging Material
Problem: Misalignment of the packaging material can lead to wasted materials and improper sealing, which can compromise the integrity of the product.
Solution: To prevent misalignment, operators should ensure that the packaging material is loaded correctly and that the machine is calibrated for the specific size and type of sachet being produced. Regularly checking the alignment guides and adjusting them as necessary can also help maintain proper alignment throughout the production run.
6. Software Glitches
Problem: Modern stick packing machines often rely on sophisticated software for operation. Software glitches can disrupt production and lead to errors in packaging.
Solution: Regular software updates and maintenance checks can help prevent glitches. Operators should be trained to troubleshoot common software issues and know how to reset the system if necessary. Keeping a backup of the software and having a technical support plan in place can also minimize downtime in case of a malfunction.
7. Wear and Tear of Components
Problem: Over time, components of stick packing machines can wear out, leading to decreased efficiency and increased risk of breakdowns.
Solution: Implementing a regular maintenance schedule that includes inspections of all moving parts can help identify wear and tear early. Replacing worn components before they fail can prevent unexpected downtime. Keeping an inventory of critical spare parts can also ensure that repairs can be made quickly.
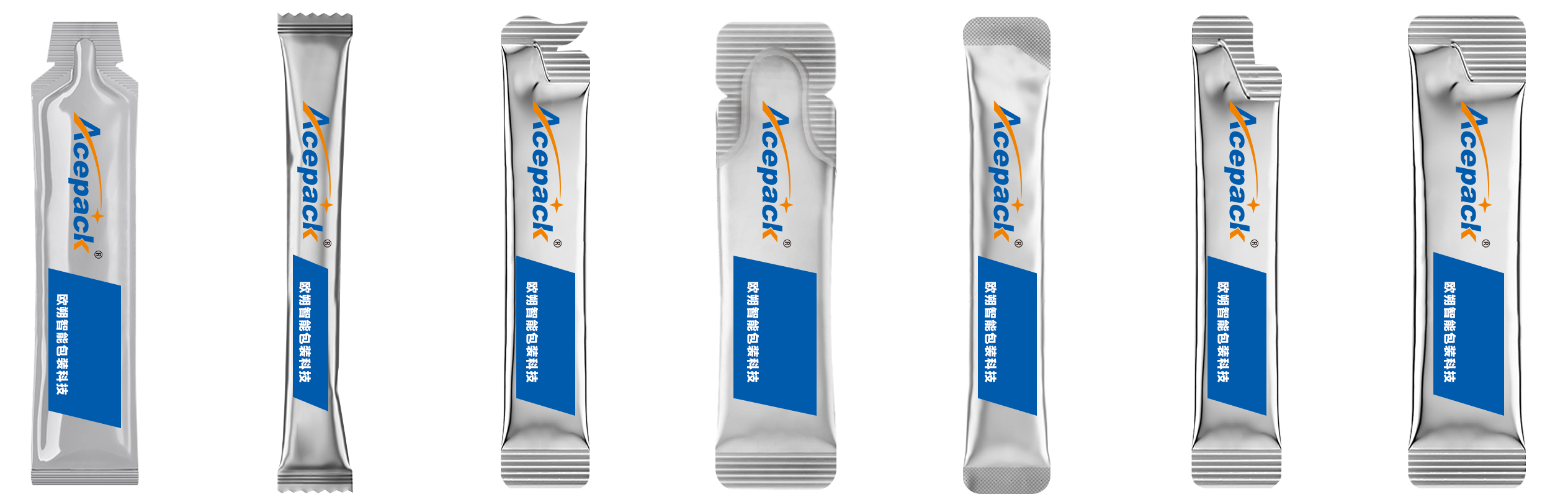
multi-lane sachet packaging machines are vital in the packaging industry. However, they are not without their challenges. By understanding common problems and implementing effective solutions, operators can enhance the efficiency and reliability of their packaging processes. Regular maintenance, proper training, and adherence to manufacturer guidelines are key to ensuring smooth operation and minimizing disruptions in production. With the right approach, businesses can maximize the potential of their packaging machinery and maintain a competitive edge in the market.